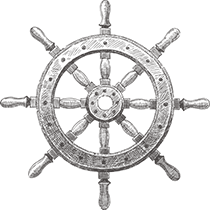
In the usual and most traditional boat building method, an infrastructure is built consisting of the keel, molds and ribbands or stringers over which frames or ribs, of oak, elm or laminations are bent and faired by careful shaving of bevels with planking thickness allowances made.
The planking is carefully lined off, cut, and fitted as tightly as possible after opening the outboard edges to accept the caulking iron, and then screwed or riveted to the frames. After this, the seams are caulked, painted, and filled with a seaming compound. This method of boatbuilding is extremely time consuming and costly, and does nothing to eliminate potential leaky seams, butt blocks and electrolysis.
Additionally, veneers are very expensive when compared to the same finished dimensions of sawn lumber and when glued up, they are over twice the weight as well.
Cold Molding - Costly and Admittedly Incorrect
Cold molding is not only very costly but it is structurally faulty. The latest thinking, now
supported, even by long and insistent advocates of the process admittedly contend that it is
incorrect to plank layer upon layer of veneers glued at right angles to each other. Wood is almost
perfectly stable in the longitudinal direction but lacks stability transversely. Therefore, the
slight but continuous unnatural directions of hygroscopic movement work to break down the fraying
surfaces of interior veneers as they roll unsympathetic surfaces against each other. This constant
plywood warfare does not occur with the Cutts Method because all the swelling of the planking
surfaces are in directional harmony with each other.
Additionally, veneers are very expensive
when compared to the same finished dimensions of sawn lumber and when glued up, they are over twice
the weight as well. The cost of the epoxy, with the other thickening agents, is $80 or more a
gallon, and most of it is swept up off the floor or inhaled as grinding dust and debris after
applying and sanding layer upon layer of unstable laminates over an expensive basket-like throwaway
mold that must be intricate enough to hold the very thin laminates fair to the shape required.
Further, clamping is a very messy business with thousands of staples shot through unruly thin veneers using sticky glue guns only to be pulled out after each application. Grinding to a fair shape must be accomplished after each layer is applied, over and over again. Experience shows that voids are left and veneers are constantly ground through where the fairing is not perfect or edges stay lifted to be ground off in fairing the surfaces of each thin layer.
The end result is a product that is excessively expensive and structurally incorrect.
A step by step comparison of the Cutts Patented Method vs. traditional methods reveals these conclusions:
The Cutts method eliminates:
<< Advantages of Cutts Method | Wood vs Fiberglass>>